3-DOF parallel delta Robot with GA based vision and path planning technique
- Manuka Suriyage
- Dec 9, 2018
- 5 min read
Updated: Jun 1, 2020
This research presents a complete methodology to design an industrial 3D delta robot based on a workspace requirement. Additionally the system is embedded with a vision based system to perform a pick and place task. The operation is optimized through a genetic algorithm (GA) based path planning technique.
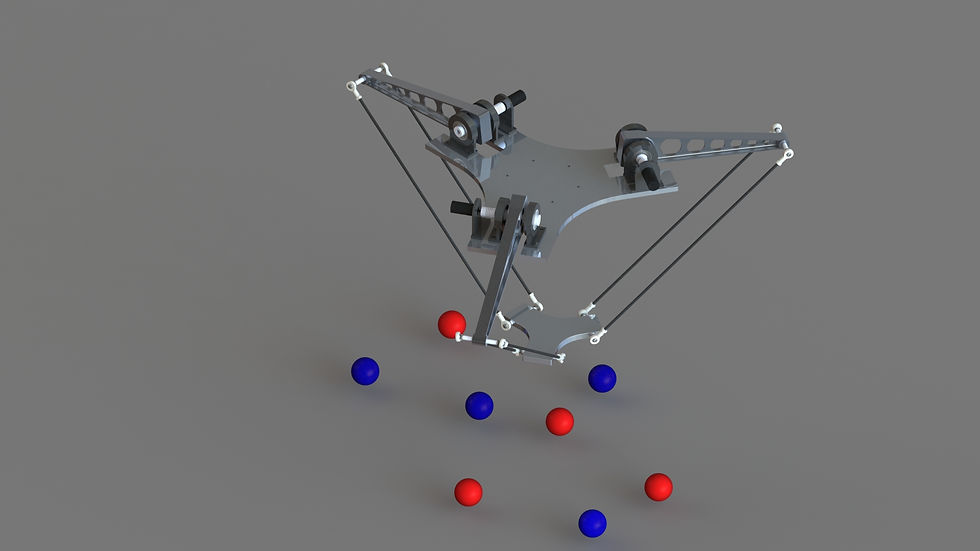
Introduction
A manipulator is fundamentally a reprogrammable, multifunctional mechanical arm intended to move parts, tools, and specialized device through preprogrammed motions for the performance of various tasks. With the advances in technology over last decades Parallel manipulator became more popular for industrial purpose. Parallel manipulators are used for variety of tasks such as material handling, 3D printing and pick and place operations.
Delta robots are parallel type of robots which are capable of performing high-speed movements accurately in a limited workspace. This makes them highly suitable for handling light objects and most of the time these robots are used in packaging and drilling applications mainly aimed at food, pharmaceutical and electronics industry. Vision based systems are included in delta robot systems for quality grading in food industry and for classifying similar products with different colors and shapes in packaging industry.
The research introduce a design methodology for a parallel type delta robot with some novel software tools. These techniques reduce the complexity of the design process and help to optimize design parameters.The 3D modelling, structural and multi body dynamic simulations and material selection techniques were used in the design process and the design is validated through a prototype. A PID controller is designed considering the simplicity and ease of implementation.
Structural design
The design approach shown in figure 1 was used for the project development. The initial design parameters and requirements were identified based on an extensive literature study. A special MATLAB based software was developed to validate the Kinematics and Dynamics of the robot and to obtain and optimize the design parameters for the required work-space. Based on the finalized parameters the 3D model was developed using SolidWorks.

Figure 1 : Design approach
The design was carried out based on the workspace requirements for the pick and place application. The application is defined as the effective sorting of different color balls within a workspace of 11300 square centimetre circular area which is 400 mm below the base plate structure. The main parts and the 3D model design of the delta robot is shown in figure 2.

Figure 2 : Delta robot 3D model and the main parts
Several combinations of design parameters [𝐿𝑖, 𝑙𝑖 , 𝑆𝐵, 𝑆𝑃 ] can be used to achieve a required workspace. A kinematic model is developed using MATLAB to perform both kinematic simulations and workspace analysis.The software provides the parameter combination that can generate the desired workspace requirements. The software can visualize the workspace, movement of the delta robot, actuating angle combinations and inverse and direct kinematic results as shown in figure 3.
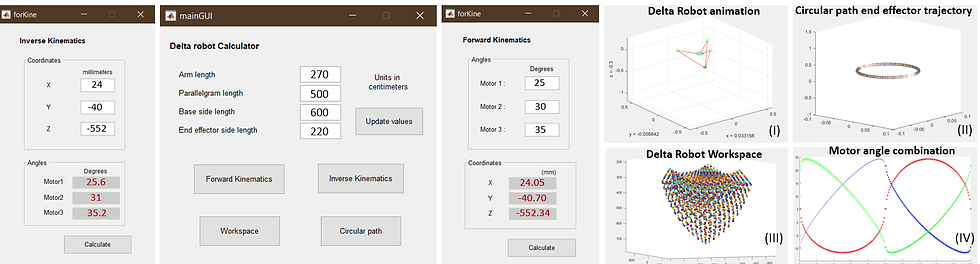
Figure 3 : MATLAB based design parameter optimization software
Multibody dynamic simulations were performed using ADMAS software to obtain the forces and torques acting on the links and joints of the delta robot. The torque results were used to select the suitable motors for the application.

Figure 4 : Adams MBD simulations
The force results were taken to perform static structural simulations and topology optimization of the robot arm design. Static structural simulations were done using ANSYS Mechanical to optimize the shapes and to select material.

Figure 5 : Static structural simulations for the delta robot arm designs
Control System design
The control system consists of a camera for optical feedback and 3 encoder gear motors. Control flow chart of the robot is shown in figure 6.

Figure 6 : Control system flow chart
The PID controller was initially designed based on the Simscape control model. But the controller was manually tuned to obtain the required accuracy.
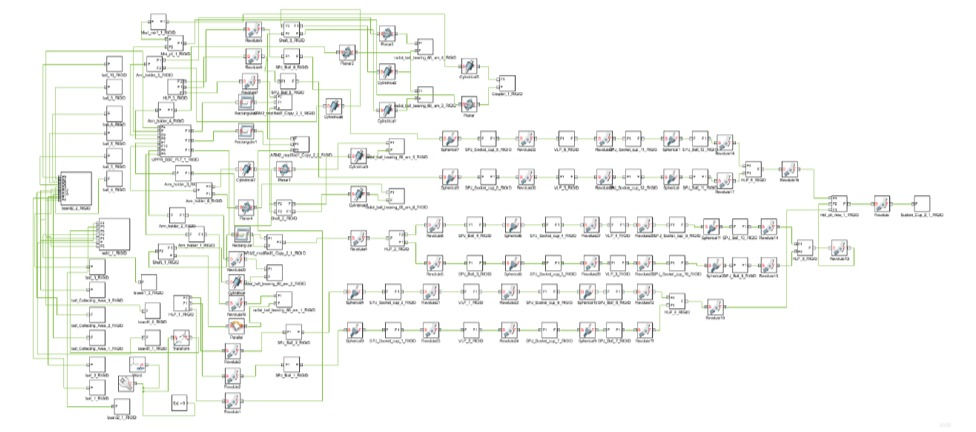
Figure 7 : Control system Simscape model
Control circuit design and simulation were done using Proteus and a simple PCB design was proposed for the control circuit as in Figure 8.

Figure 8 : Control circuit and PCB design
Fabrication
The complete fabrication process was carried out at University of Moratuwa Mechanical Engineering department. The three main robot arms were fabricated using CNC technology. All other components were manufactured manually by the group Members.

Figure 4 : Robot parts manufactured using CNC and manual machining
Vision based path planning system design
The camera-based vision system can detect the color of objects in the field of view of the camera using HSV scales and maps the center of gravity of each object using image processing algorithms. The centers of gravity serve as nodes in the path planning procedure along with the color of the objects to determine the pick-and-place sequence of objects using genetic algorithm. Based on the pick and place sequence the end effector position sequence is determined and inverse kinematics is used for calculating the joint actuating angles. PID motor position controlling is used for controlling the end effector position and multithreaded programming is enabled for simultaneous control of the 3 motors efficiently.
The Genetic algorithm based sorting technique proposed in this project was presented in the ICCAR conference held in singapore on April 2020. The publication will be added to the digital library in the near future and it contains a complete description on the optimization algorithm.
Conclusion
A design approach for a parallel robot development is proposed through this research with some novel tools. A MATLAB based software was successfully developed to optimize the design parameters of a delta robot and to check inverse and direct kinematics. The prototype was fabricated and the design was justified using the prototype. The mechanical design was capable of handling the expected payload and had the capability to work on the designed work-space.
Furthermore a color and size sorting algorithm was proposed using OpenCV-Python for an industry emulated scenario. The algorithm can be used for real time dynamic object tracking. The color accuracy of the camera affects the overall performance of image processing while evenness of lighting condition in the field of view of camera gives better results. Distortion effects have not been considered. A proper calibration procedure must be followed to decide the scale factors, translation vectors and rotation angles when defining the transformation matrix from camera coordinate frame to the base coordinate frame of the robot.The developed sequence optimization algorithm can be easily adapted to pick-and-place sequence optimizing problems in the industry irrespective of a specific application. Future work will be to optimize and find suitable GA parameters so that the user can define the parameters without any prior experience or knowledge

Figure 5 :Prototype
Manual control and image processing based automatic sorting was tested using the prototype. The optimization algorithm performance is expected to be further improved.
more information on the publications and conferences can be found in the following link:
ICCAR conference singapore 2020 : Genetic Algorithm Based Pick and Place Sequence Optimization for a Color and Size Sorting Delta Robot.
Other group members:
Supervised / Advised by:
Special acknowledgement:
Comments